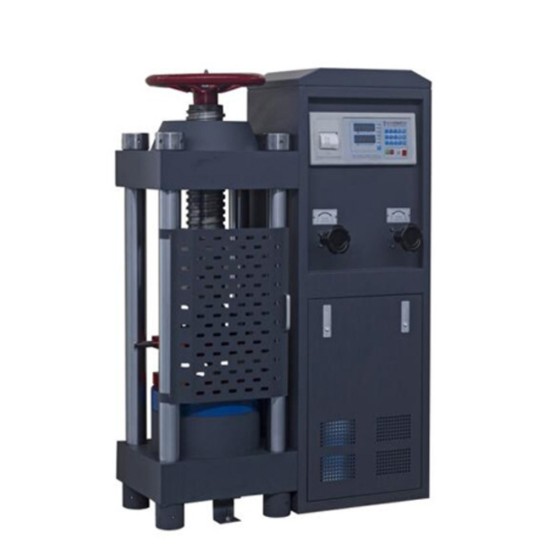
- Stock: In Stock
- Model: YES 2000
- Weight: 750.00kg
- Dimensions: 88.00cm x 48.00cm x 140.00cm
Available Options
Product description:
This testing machine is mainly used for compressive strength testing of building materials such as bricks, stones, cement, and concrete, and can also be used for mechanical performance testing of other materials.
This machine is equipped with electric hydraulic loading, sensor force measurement, digital display of force values, printer printing of force data, and conversion of compressive strength. This testing machine complies with national standards, manually controls the loading speed, and has functions such as loading speed display, peak holding, and overload protection. It is an essential testing and detection equipment for construction, building materials, highway and bridge engineering units.
Structure Introduction:
The body of the testing machine is connected to the upper beam by four columns, and an adjustment screw is installed on the upper beam of the testing machine. The large handwheel and nut screw can adjust the no-load height of the testing machine. The lower end of the screw is equipped with a ball seat and an upper pressure plate. The lower pressure plate is placed on the piston of the oil cylinder. When the test piece contacts the upper pressure plate, the ball seat of the upper pressure plate can self adjust and balance, keeping the test piece level with the upper and lower pressure plates. There are notches for the positioning of the test piece engraved on the lower pressure plate. During the test, the test piece should be aligned with the notches. There is a dust cover under the lower pressure plate to prevent or reduce dust from entering the oil cylinder and damaging the cylinder or oil seal during piston lifting. There is a sealing device between the piston and the oil cylinder to prevent Oil spill. However, when there is still a small amount of Oil spill from the piston during use, there is a ring shaped oil groove at the top of the cylinder block, and there is a drain channel to discharge the oil and return to the oil tank.
The hydraulic control part of the control box of this testing machine mainly consists of a fuel tank, oil pump, oil filter, electric motor, oil delivery valve, return valve, etc. The oil pump is a direct rotation shaft plunger pump. When the testing machine is loaded, the loading oil delivery valve should be manually controlled to restore control of the piston's rising speed (this speed is integrated with the safety valve). When unloading, the return valve can be turned, and the oil cylinder will slowly descend. The safety valve of the testing machine has been adjusted to the appropriate position before leaving the factory. Users cannot adjust the safety valve during normal use.
Quality Assurance Period (QAP) Explanation
1. The Quality Assurance Period (QAP) is an important aspect of our commitment to ensuring the quality and reliability of our products. We understand that customers rely on our goods to function properly and meet their expectations. To demonstrate our confidence in our offerings, we provide a warranty period during which we take responsibility for any quality issues that may arise.
2. The length of the warranty period varies depending on the type of product. Generally, for consumable components subject to wear and tear, such as abrasion parts, the warranty period is three months. For smaller components, the warranty period is typically extended to six months. As for major equipment and machinery, we offer a one-year warranty period.
3. We also recognize that each customer's requirements may differ, and we are open to negotiation regarding the warranty period. If the buyer requests a specific warranty duration that differs from our standard policy, we are willing to discuss and accommodate their needs accordingly.
4. During the warranty period, we take full responsibility for any quality-related issues that arise. If a product is found to be defective or malfunctions due to manufacturing or material faults, we are committed to providing a resolution. This includes either replacing the faulty component or conducting necessary repairs to restore the product to its intended functionality. Our aim is to minimize any inconvenience caused to our customers and ensure their satisfaction.
5. It is important to note that the warranty does not cover damages resulting from improper use, mishandling, or normal wear and tear. Additionally, if any modifications or repairs are carried out by unauthorized personnel during the warranty period, the warranty may become void.
6. At our company, customer satisfaction is our top priority. We strive to provide high-quality products that meet and exceed expectations. The Quality Assurance Period serves as a testament to our commitment to delivering reliable solutions and ensuring that our customers have peace of mind when choosing our products.
Transportation:
1. We offer various trade methods, including EXW, FOB, CIF, DDU, DDP, etc., allowing customers to choose the most suitable option based on their requirements.
2. We consider the proximity to the factory where the goods are located when selecting the appropriate port of departure.
Customers can provide the destination port where the consignee is located or choose a designated port for delivery.
3. Our transportation methods encompass a wide range of options, including waterway transportation, air transportation, and courier services such as DHL, FedEx, EMS, UPS, TNT, etc.
For waterway transportation, we work with reputable shipping companies such as APL, CMA, CNC, COSCO, EMC, EVERGREEN, HMM, KMTC, MCC, MSC, MSK, ONE, SITC, YML, etc.
Air transportation is available through airlines such as (Air China): CA; (China Southern Airlines): CZ; (China Eastern Airlines): MU; (Garuda Indonesia): GA; (Cathay Pacific Airways): CX; (Cathay Dragon): KA; (Korean Air): (Japan Airlines): JL; (Singapore Airlines): SQ; (Thai Airways International): TG, and more.
4. The transportation time will vary depending on the destination and the chosen transportation method. We will communicate and confirm the estimated time of arrival with the customer prior to shipping.
5. Shipping costs are influenced by factors such as transportation method, weight, size, and destination. We provide shipping cost estimation services to assist customers in budgeting.
6. Once the goods are shipped, we offer order tracking services to provide customers with detailed information about the whereabouts of their shipment. Additionally, based on the selected trade method, we can arrange cargo insurance to provide compensation in the event of loss or damage during transportation.
7. The specific transportation arrangements mentioned above will be coordinated by dedicated personnel, taking into account the actual situation and policies. We strive to tailor the optimal and most cost-effective shipping plan based on the information provided by the customer.
Please note that we are committed to ensuring the smooth transportation of goods and will work closely with customers to address any specific requirements or concerns they may have regarding transportation.